For many months I have been preparing for a show at The Artery in Davis, CA. The Artery is an a cooperative gallery with about 70 member artists and I have sold my work there for over ten years. The show runs from November 7 to December 1. I hope that local people will be able to visit.
Jacob blankets above and on the rocking chair (my mom's) on the right. Gray blanket on the left chair uses "Mom's yarn" (see a future blog post on that). The others are wool from other Solano County farms.
The best way to explain this show is to reprint my "Artist's Statement" here. My blog is usually mostly photos because that's the kind of blog that I like to read but I hope that you will take the time to read the following because it explains the concept behind the work in the show. I'll throw in a few photos, but will display others in later blog posts.
Blankets woven from yarn grown by Imperial Stock Ranch in Oregon.The story about this yarn will be in a later post.
Artist's Statement: In 2010 I became involved in the Fibershed movement by donating yarn produced from my flock of Jacob sheep to Rebecca Burgess whose goal was to wear, for a year, only clothes sourced entirely from an area within 150 miles of where she lived. That means that the fiber (and any dye) was grown, the yarn was spun, the cloth created, and the garment sewn locally! Imagine doing that—it’s not easy!
Why bother? Have you looked at your clothing labels and thought about the impacts of the way in which we clothe ourselves? The true cost of inexpensive clothing is high when you consider the social and environmental impacts on a global scale. (China produces 52% of the world’s textiles.)
Rebecca’s personal challenge led to the creation of the on-line Fibershed Marketplace in 2011, and in 2012 the Fibershed (501c3) with the mission “... to change the way we clothe ourselves by supporting the creation of local textile cultures that enhance ecological balance, and utilize regional agriculture while strengthening local economies and communities.” In other words, by embracing the Fibershed concept, we support the idea of using locally grown and locally made textiles and encouraging the development of Fibersheds all over the world.
Education is an integral part of the Fibershed movement—educating the consumer about the environmental, economic, and social benefits of embracing the Fibershed concept. Imagine the Slow Food movement applied to textiles!
Close to Home... Does that mean down the block, across town, or within the U.S.A? Each yarn used in this show has a story. Some were grown by my own sheep, some by my neighbors, and some in other parts of Solano County. One is grown by a long-established Oregon ranch and another is grown by several ranches in the Pacific Northwest and dyed with plant dyes in Napa County. A few pieces are woven of yarn handspun and dyed by my mom many years ago. It was a challenge to stay true to the Fibershed concept when I needed commercial fabrics for pillows. (One of the many Fibershed goals is to bring mills back to our area that will commercially produce fabrics not locally produced now.) I did the best I could by using fabric and pillow forms made in the U.S.A. and some pillows use my home-grown wool for the pillow itself.
I wove or felted all the wool fabric in the show and each of the fibers have a story. Some were grown close to home and other evoke memories of home. The pieces are simple because my focus is on the fiber and the yarn. Enjoy the photos, read the stories, and think about the stories that your textiles would tell.
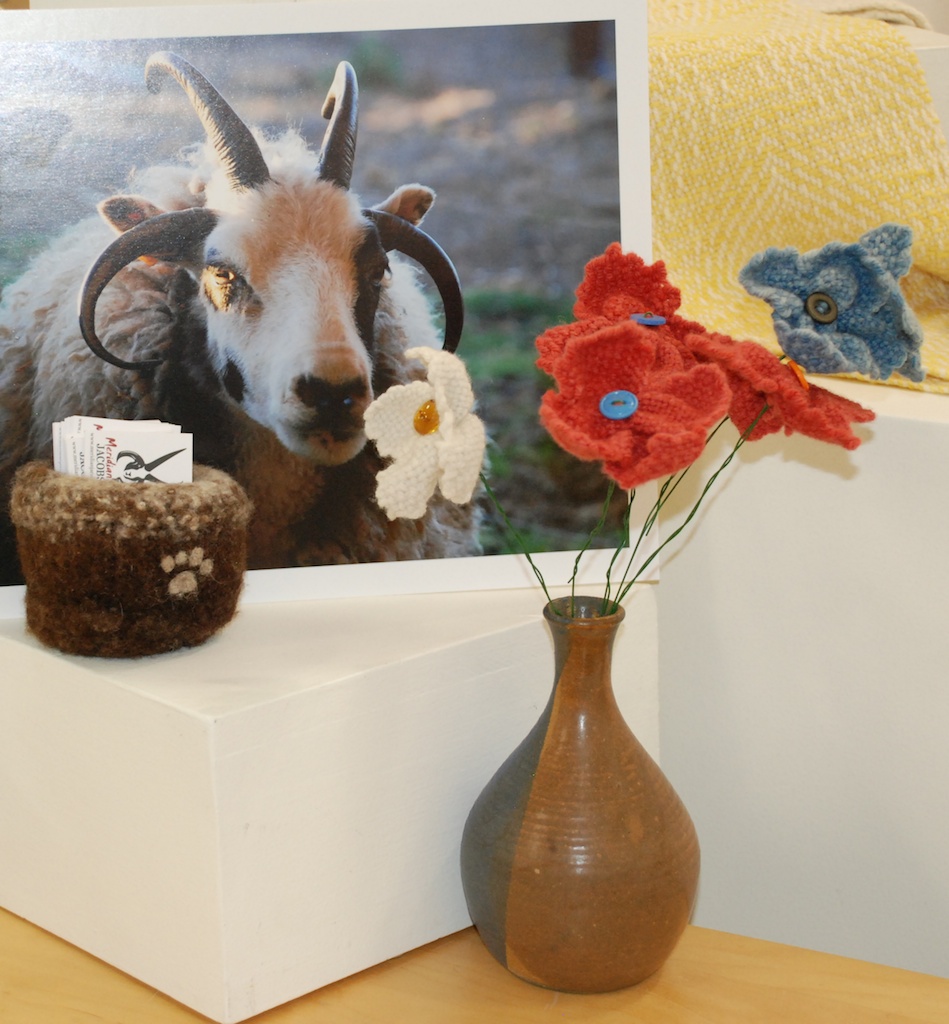